Heat Transfer Between Impinging Circular Air Jet and Finned Flat Plate and Validation of Results Using Artificial Neural Network
R.E. Shelke¹* and L. B. Bhuyar²
¹Government I.T.I. Morshi Road, Amravati - 444 603 (India)
²Department of Mechanical Engineering PRM Institute of Technology and Research, Badnera Amravati - 444 701 (India)
Article Publishing History
Article Received on :
Article Accepted on :
Article Published :
Article Metrics
ABSTRACT:
Impinging jets on rough surfaces are important in many industrial applications. The surface may become rough for many reasons. Roughness may arise from manufacturing processes, a long time in service and/or natural occurrences such as rain, snow, frost etc. Prior research indicate that the average roughness height on in-service gas turbine blades may vary from 1.5um to 10um.This is very rough considering the thickness of the boundary layer is of the order of 1 mm.Similarly,there are some industrial applications like spray formed billet cooling by impinging jets where the target and the jet are not orthogonal but the oblique.Therefore, study of inclination of target plate on heat transfer between impinging jet and rough flat plate is important. In the present work, inclination effect is studied for the oblique angles of 45°, 60° and 75° at a given Z/D of 1 and Reynolds number of 23000. The rough surfaces are in the form of hexagonal prism of side 2.04 mm and height of 2 mm spaced at a pitch of 7.5 mm on the target plate.The experimental results are validated using Artificial Neural Network (ANN).It has been observed that the validation using ANN gives the correlation coefficient (R²) as 0.998 to 1.
KEYWORDS:
Impinging Air Jet; Heat Transfer; Hexagonal Finned Surface; Artificial Neural Network (ANN)
Copy the following to cite this article:
Shelke R. E, Bhuyar L. B. Heat Transfer Between Impinging Circular Air Jet and Finned Flat Plate and Validation of Results Using Artificial Neural Network. Orient. J. Comp. Sci. and Technol;2(1)
|
Copy the following to cite this URL:
Shelke R. E, Bhuyar L. B. Heat Transfer Between Impinging Circular Air Jet and Finned Flat Plate and Validation of Results Using Artificial Neural Network. Orient. J. Comp. Orient. J. Comp. Sci. and Technol;2(1). Available from: http://www.computerscijournal.org/?p=2104
|
Introduction
Impinging jets have received considerable attention due to their inherent characteristics of high rates of heat transfer besides having simple geometry. Various industrial processes involving high heat transfer rates apply impinging jets. Heat transfer rates in case of impinging jets are affected by various parameters like Reynolds number, nozzle plate spacing, radial distance from stagnation point, Prandtl number, target plate inclination, confinement of the jet, nozzle geometry, curvature of target plate, roughness of the target plate, low scale turbulence intensity i.e., turbulence intensity at the nozzle exit. Gardon and Cobonpue¹ have reported the heat transfer distribution between circular jet and flat plate for the nozzle plate spacings greater than 2 times the diameter of jet, both for single jet and array of jets. They have used specially designed heat flux gauge for the measurement of local heat transfer rates from a constant wall temperature plate. Gardon and Akfirat² studied the effect of turbulence on the heat transfer between two dimensional jet and flat plate. They also studied effect of multiple two-dimensional jets on the heat transfer distribution.3 Baughn and Shimizu4 and Hrycak5 have conducted experiments of heat transfer between round jet and flat plate employing different methods of surface temperature measurement. Lyttle and Webb6 have studied the effect of very low nozzle plate spacing (Z/D < 1) on the local heat transfer distribution on a flat plate impinged by a circular air jet and found that in the acceleration range of the nozzle plate spacing (Z/D < 0.25),
maximum Nusselt number shifts from the stagnation point to the point of secondary peak with the effect being more pronounced at higher Reynolds number. Experimental work on impinging jets is done by Martine,7 and Viskanta9 alongwith review by Jambunathan et. al.8.Hansen and Webb10 have studied the effect of the modified surface on the heat transfer between impinging circular nozzle and the flat plate.
The present knowledge of heat transfer concerning an impinging jet on the inclined rough surfaces is inadequate. So, in the present work, inclination effect is studied for the oblique angles of 45°, 60° and 75° and at a given Z/D of 1 and Reynolds number of 23000. The fins used are hexagonal prism of side 2.04 mm and height of 2 spaced at a pitch of 7.5 mm on the target plate. The experimental results are validated using Artificial Neural Network.
Artificial Neural Network
Artificial neural network is a data processing system consisting of a number of simple, highly interconnected processing elements in an input/output architecture.12-13 ANNs have found varied applications in the field of heat and mass transfer. ANNs are massively parallel, distributed and adaptive system, modeled on the general features of biological networks with the potential for ever improving performance through a dynamical learning process. Neural networks are made up of great number of individual processing elements, the neurons, which perform simple tasks. A neuron is the basic building block of neural network technology, which performs a nonlinear transformation of the weighted sum of the incoming inputs to produce the output of the neurons.
Neural networks are comprised of a great number of interconnected neurons. There exists a wide range of network architectures. The choice of the architecture depends upon the task to be performed. For modelling of a physical system, a feed forward layered is usually used. A feed forward neural network, which is the most common neural network type, consists of layer of input neurons, and one or more hidden layers. The connections are typically formed by connecting each of the nodes in a given layer to all the neurons in the next layer.
In this way every node in a given layer is connected to every another node in the next layer. The input layer does no processing, it is simply where the data vector is fed into the network. The input layer then feeds into the hidden layer. The hidden layer in turn, feeds into the output layer. The actual processing in the network occurs in the nodes of the hidden layer and the output layer.
Experimental
Air jet is supplied by a three-cylinder two-stage air compressor through a calibrated orifice flow meter. Air filter and Pressure regulator are installed upstream of the orifice flow meter to filter the air and to maintain the downstream pressure at a value of 4±0.005 bar. The flow rate is controlled by two needle valves, one on each side of the orifice flow meter. The nozzle, which directs the air until it impinges upon a heated target plate, is constructed with a 7.3 mm inner diameter aluminum pipe of length to diameter ratio of 83. The impinging plate is constructed using 1 mm thick stainless steel plate of size 120 mm x 120 mm. Nichrome heater of size 100 mm x 100 mm is packed between impinging plate and a bakelite support plate with mica sheets to isolate the impinging plate from the heater electrically. Electric power is supplied to the heater through variac. The voltage and the current are measured by digital panel meters. Thermo couples are attached on finned surface along the flow direction to measure the wall temperature distribution.
Results and Discussion
Figure 1 shows the effect of inclination on the heat transfer for smooth and hexagonal finned surfaces at different oblique angles of 45°, 60° and 75° at given Z/D of 1 and Reynolds number of 23000. It can be observed that when the target plate is kept inclined to the axis of the jet; acceleration side (Uphill side, θ = 0°) exhibits higher heat transfer than that on the downhill side (θ = 180°). For the smooth surface Figs.1 (a), (b) and (c)), near the stagnation point, the heat transfer data shows more or less axisy metric nature up to r/D of 1 to 1.5 for all oblique angles studied. At an oblique angle of 45°, the scattering in the heat transfer data on uphill and downhill side is maximum. For rough surfaces, Figs. 1 (d), (e) and (f) show that the scattering in the heat transfer data for uphill and downhill sides is more that the corresponding case of the smooth surface.
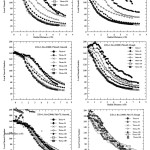 |
Figure 1: Effect of inclination on the Nusselt number for smooth and hexagonal finned surface at Z/D of 1
Click here to View figure
|
These experimental results are validated using Artificial Neural Network in the present study. The observed values are compared with predicted values obtained by Artificial Neural Network for hexagonal finned surface at various parameters. Fig. 2 shows the RMSE values for hexagonal finned surface at Z/D = 1 , Re = 23000 and Phi=450 .On the uphill side, validation using ANN gives the correlation coefficient (R2) as 0.998. After training the Artificial Neural Network, it is found that every case of the experimental observations at oblique angles of 60° and 75° is also in the good agreement with the predicted values obtained by ANN. The correlation coefficient (R²) for every case tested is found to be in the range of 0.998 to 1.It means that the perfect validation is carried out in experimentally observed values and values predicted by Artificial Neural Network.
Conclusions
The inclination of the target surface with the axis of the jet causes the scattering of the heat transfer coefficient between the impinging jet and the flat plate on the acceleration side and the compression side. The acceleration side exhibits higher heat transfer than the compression side, particularly, away from the stagnation point (r/D > 1.5) for the smooth surface. For the rough surface, scattering in the heat transfer data is observed also in the stagnation region. There exists the shift in the point of maximum heat transfer from the geometric stagnation point toward the acceleration side for the rough surface. No such shift is observed for the smooth surface. After training the Artificial Neural Network, it is found that every case of experimental results is in good agreement with the predicted values obtained by ANN. The coefficient of correlation (R²) for every case tested is found to be in the range of 0.998 to 1, which suggest the validation of experimentation carried out in the present work.
References
- R. Gardon and J. Cobonpue, Heat Transfer Between a Flat Plate and Jets of Air Impinging on It, Int. Developments in Heat Transfer, ASME 454-460 (1962).
- R Gardon and C.Akfirat, The Role of Turbulence in Determining the Heat Transfer Characteristics of Impinging Jets, Int. J. Heat and Mass Transfer,8:1261- 1272 (1965) .
- R Gardon and C. Akfirat, Heat Transfer Characteristics of Impinging Two Dimensional Air Jets”, J. of Heat Transfer, 88: 101-108 (1966).
- J. W. Baughn and S. Shimizu, ” Heat Transfer Measurements From a Surface With Uniform Heat Flux and an Impinging Jet”, J. of Heat Transfer, 111:1096-1098 (1989).
- P. Hrycak, Heat Transfer from Round Impinging Jets to a Flat Plate, Int. J. Heat Mass Transfer, 26:1857-1865 (1983).
- D. Lytle, B. W. Webb, Air Jet Impingement Heat Transfer at Low Nozzle Plate Spacings, Int. J. Heat and Mass Transfer,37:1687-1697(1994).
- H. Martine, Heat and Mass Transfer between Impinging Gas Jets and Solid Surfaces, Adv. Heat Transfer, 13:1-60 (1977).
- K. Jambunathan, E. Lai, M. A. Moss, B.L. Button, A Review of Heat Transfer Data for Single Circular Jet Impingement, Int. J. Heat and Fluid Flow,13:106- 115 (1992).
- R. Viskanta, Heat Transfer to Impinging Isothermal Gas and Flame Jets, Experimental Thermal and Fluid Science, 6:111-134 (1993).
- L. G. Hansen, B. W. Webb, Air Jet Impingement Heat Transfer from Modified Surfaces, Int. J. Heat Mass Transfer, 36: 989-997 (1993).
- W. M. Chakroun, A. A. Abdel-Rahman, S. F. Al-Fahed, heat transfer augmentation for air jet impinged on a rough surface, Applied Thermal Engineering, 18: 1225-1241 (1998).
- Schalkoff R.J.,”Artificial Neural Network.”, McGraw-Hill,International Edition, (1997).
- LiMin Fu, ” Neural Network in Computer Intelligence .” Tata McGraw-Hill, (2003).

This work is licensed under a Creative Commons Attribution 4.0 International License.